An eddy current brake is a non-contact braking system, most commonly used in trains and roller coasters. In an eddy current brake, magnets are used to induce eddy currents in a metal rotor or another metal part of the vehicle. According to Lenz’s law, those induced currents create a magnetic field opposing the original field. The two opposing magnetic fields work to slow the vehicle in contrast to the frictional force used in a traditional braking system.
Chris Gaffney and Adam Catching’s article “Magnetic Viscous Drag for Friction Labs,” in the September 2016 edition of The Physics Teacher describes their investigation into eddy current braking. As an alternative to a traditional friction lab, their students slide magnets down a long aluminum ramp. The magnets are slowed by the eddy currents they induce in the ramp.
As a company that sells a lot of aluminum dynamics tracks, it seemed natural for us to try this out. We designed and 3D-printed a simple magnet holder for our plastic Dynamics Cart and Track System (DTS) carts. It holds up to four magnets about 2 mm off the surface of the dynamics track.
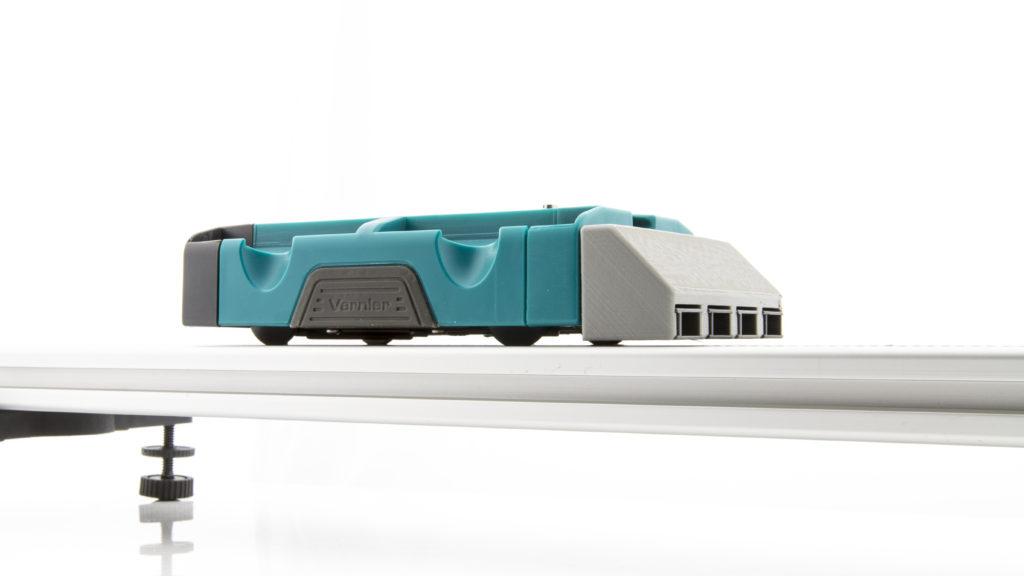
The graph shows the velocity of a DTS cart rolling on an inclined track, with either the eddy current brake (zero, two, or four magnets) or our Friction Pad installed. With zero magnets, the cart’s velocity increases linearly, as expected. With the Friction Pad installed on the cart, the velocity curve is similarly linear—albeit with a shallower slope. The shape of the velocity curve differs when the eddy current brake is installed. As expected, the induced drag on the cart increases with the number of magnets installed. It is also apparent that the nature of the eddy current braking force is different than simple kinetic friction. For example, with four magnets installed the cart reaches terminal velocity within four seconds.
The coefficient of friction, a measure of how easily two surfaces slide past one another, depends on the surfaces in contact and the normal force on the cart. In this case, the normal force is determined by the weight of the cart and the angle of the track. Neither factor varies, so kinetic friction is constant during the motion down the ramp. Thus, the velocity increases steadily, much as it would without the Friction Pad, but at a lower rate.
However, the model for the induced magnetic drag on the cart depends on the velocity of the cart. The faster the cart moves, the greater the induced eddy currents and the greater the drag. At terminal velocity, the drag has increased to the point that the acceleration of the cart drops to zero.
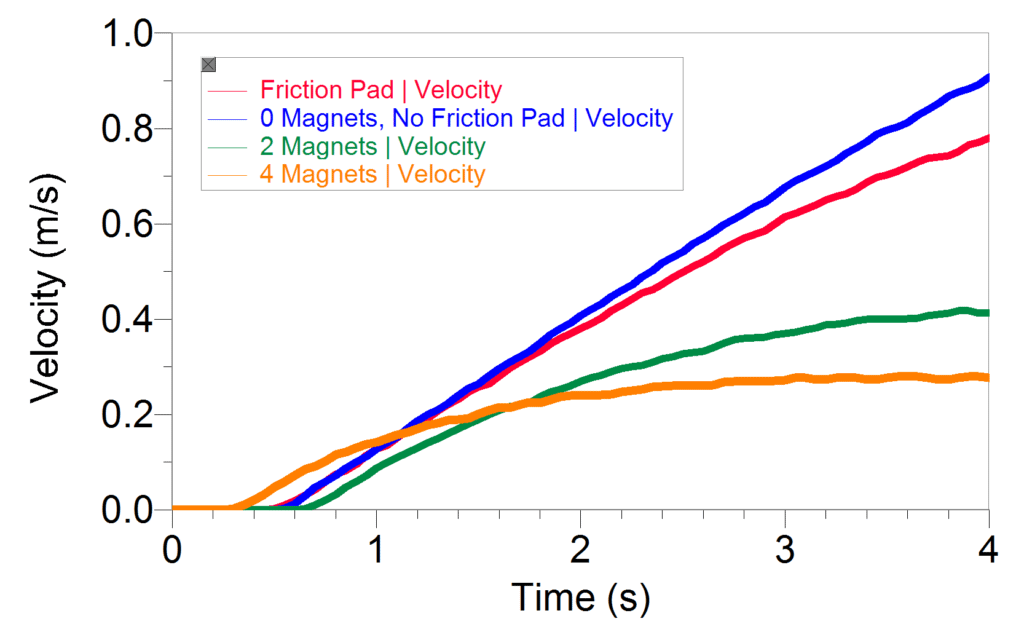
If you would like to investigate eddy current braking with DTS carts and tracks, you can 3D print your own brake. You will find the design on our Thingiverse page.