The Force Plate, like any sensor, has a limit to how quickly it can respond to a change. If a very short impulse is applied to the force plate, it will vibrate, or ring, for a short while. That ringing can interfere with your measurement.
Revised (FP-BTA) and Go Direct Force Plate
The current version of the Force Plate (
If the actual impulse period is shorter than 20 ms, the data will not reflect that due to the ring frequency. Sampling faster will not provide additional resolution.
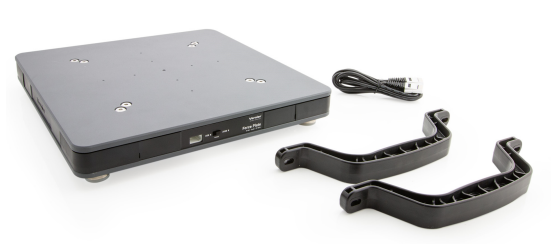
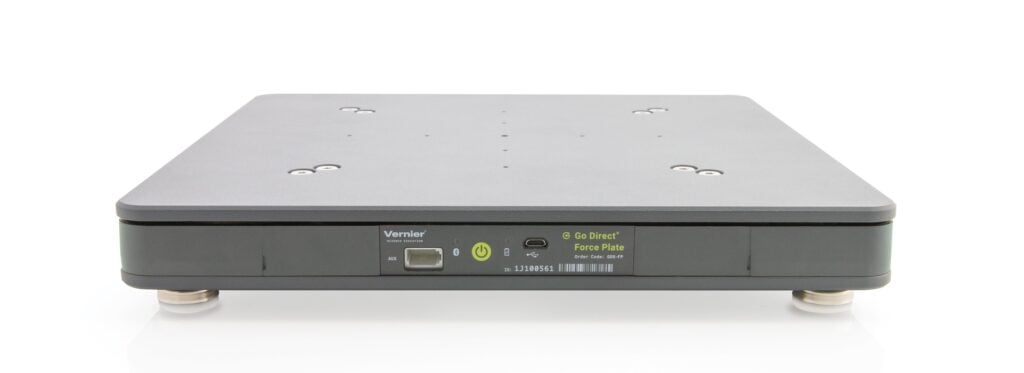
Original (FP-BTA) Force Plate
The original version of the Force Plate (those shipped before November 10, 2023) uses different load cells that have a ringing frequency of ~250 Hz, with a ~4 ms period. Even a 10 or 20 ms impulse will be distorted by the finite response time of the force place. In order to really see the structure of an impulse, the impulse should be ~200 ms or longer.
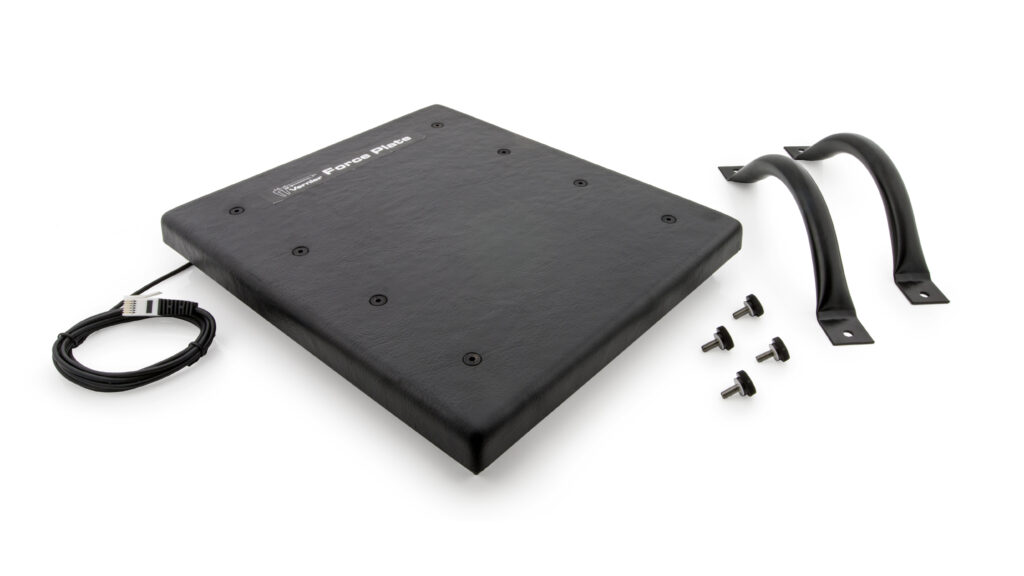
This means that you can bounce a soft, squishy balls off of the force plates and see the details of the impulse. If, however, you attempt to measure the impulse of a hard ball bounce, such as baseball or a golf ball, your data will be adversely affected by the ring frequency.